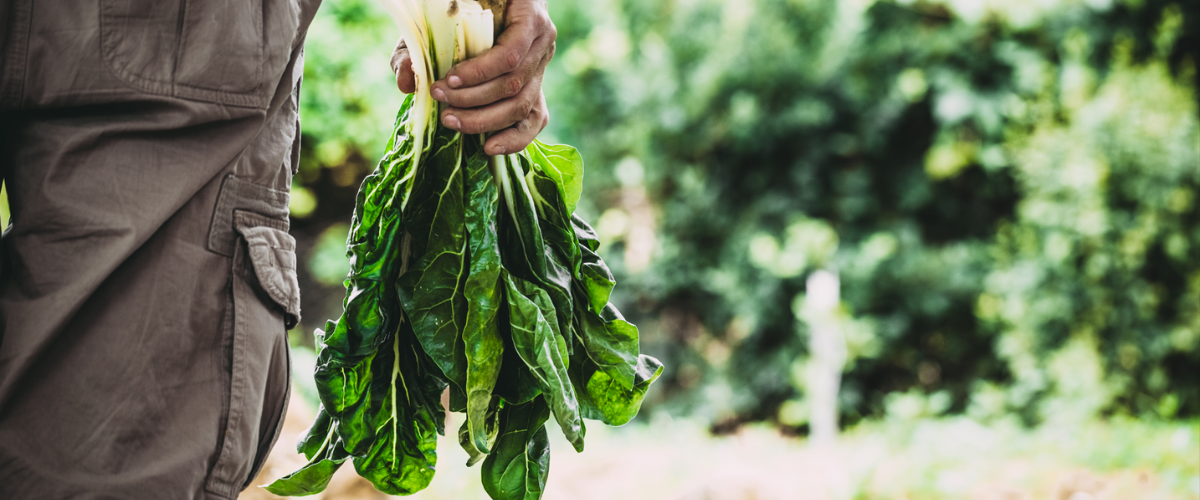
AUSVEG Advocacy: Unprecedented rises in global production costs
28 September 2023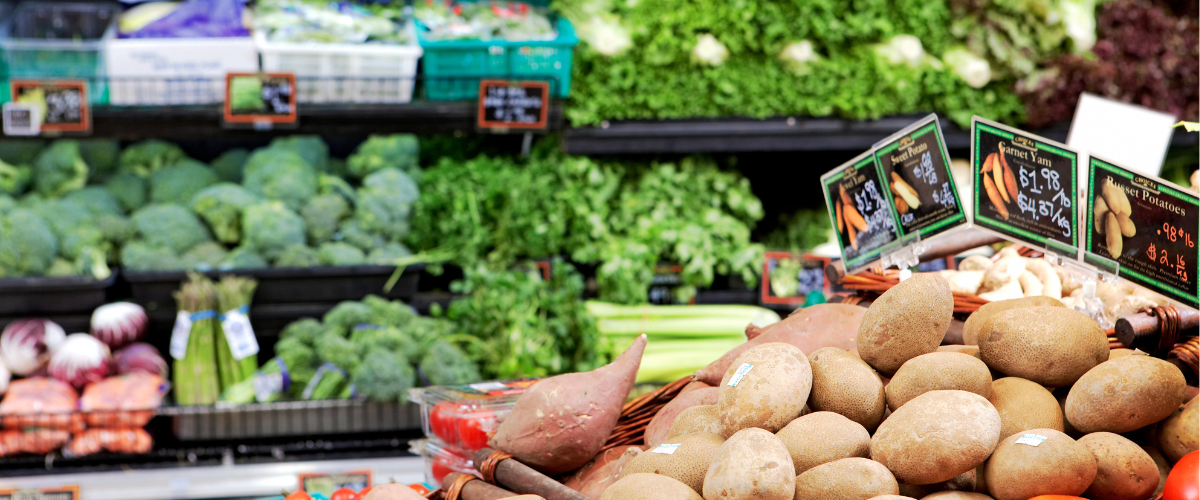
AUSVEG Advocacy: Pricing & Inputs
13 November 202330 October 2023
In October, 13 Australian growers and industry representatives travelled to the UK and EU as part of the ATMAC European Study Tour to investigate commercial and compliance drivers such as food safety, farm sustainability and ethical farming certification schemes.
Some of the schemes the group saw being implemented in farms and processing facilities in the UK and EU included Red Tractor, LEAF, GlobalG.A.P, BRCGS, SMETA and GRASP.
The United Kingdom and Europe, like Australia, have faced crippling workforce shortages in recent years. Growers have addressed workforce shortages through various mechanisms, including seasonal labour migration, attracting and retaining local employees, automation, and lean management practices including ‘upsizing’.
Working hours
One clear contrast is very evident from our study tour – overtime is king in the UK. Whilst employers like it, the employees, it could be said, demand it – specifically the large number of migrant workers from Eastern Europe or Central Asia. Unlike Australia, however, overtime conditions in the UK or Europe do not have the onerous penalty rates which have led to overtime becoming unaffordable here.
Patterns of work hours across the businesses we saw varied, although most tended to have 10-12 hour shifts. After working a standard 40-48 hours, most migrant workers were keen to fill any other roles and push their weekly hours up to around 60. Some of the businesses capped the hours any employee could work, and in some instances maximum working hours were capped by supply chain rules (i.e. retailer or certification scheme requirements).
Migrant workers wanted as many hours as possible so when they returned to their homeland they were ‘cashed-up’. Employee surveys also reflected job satisfaction was directly linked to wages earned.
Piece rate was also still a popular payment method, with workers guaranteed the minimum wage and piece rate allowing them to earn more. Some harvest worker ‘gangs’ returned year-on-year. One gang we saw was back for their eighth year, and their average hourly rate for the 2023 season was over £16, well over the minimum award wage of £10.42.
Seasonal Worker Visa
With food security and farm viability in the UK a real threat due to lack of workers, the Seasonal Worker Visa was introduced as a pilot in 2019 and has continued to grow. With an initial 30,000 visa cap, the cap for the number of workers through the program is now 45,000.
The Seasonal Worker Visa permits migrants to work in horticulture in the UK for a maximum of six months, before returning home for a minimum of 6 months. Migrants can reapply for another visa to return to the UK up to 3 months before re-entering the country. Migrants are required to have a sponsor and are issued a Certificate of Sponsorship by the ‘approved scheme operator’, of which there are six contracted under the visa scheme.
Traditionally, many of the migrant workers employed in horticulture arrived from Eastern Europe. However, with the Ukraine-Russia war and rising socio-economic levels in countries such as Poland which is attracting workers to stay in their own country, there has been a trend toward seeking workers from what is referred to as the ‘Stan’ countries; countries such as Kyrgyzstan and Kazakhstan.
Growers (employers) are regularly audited by the Home Office and the Gangmasters and Labour Abuse Authority (GLAA). Workers must be treated fairly according to all relevant legislation, visa requirements and sponsor obligations. Further to the regulatory requirements, there are often additional requirements that employers must implement to comply with certification schemes.
Permissible deductions and appropriate level of deductions were regulated and audited by Home Affairs and the GLAA. Employers largely appeared to pay up-front for location of workers from their home country to the UK.
The use of self-contained caravans (with kitchens and bathrooms) appeared to be the most popular accommodation choice for both employees and employers. The establishment of on-site caravans also diminished the demand for locally sourced accommodation, which employers recognised had the ability to push up demand and rental prices, and cause issues with local residents.
Growers have a range of staff to look after migrant workers, supporting them to make their time in the UK feel like a “home away from home”. Employees had the ability to plant gardens and personalise their caravans, whilst employers provided games, sporting facilities, laundry facilities, local town trips and other activities. Some of the employers established on-farm shops selling traditional migrant groceries and other essential supplies. This was all largely in an effort to encourage migrant workers to return to the same employer year after year.
Modern slavery and unethical treatment of workers
As in Australia, unethical treatment of workers by a small minority of rogue employers does occur, and appears to be largely driven by organised crime. Reputable growers finding themselves on the front page of a British tabloid is their worst nightmare, so their commitment to ethical treatment of workers’ schemes and certifications is an unnegotiable priority. Large growers such as G’s Fresh and Barfoots have thousands of workers on multiple sites across the United Kingdom, so ensuring the welfare of their workers in no easy feat.
G’s alone have seven managers in their ethics team, all fully trained to SA800 (Social Accountability certification) and responsible for training every single G’s employee on modern slavery (from seasonal migrant to CEO) and undertaking hundreds of employee satisfaction surveys on an annual basis. Growers also audited their supply chain, including the approved operators under the Seasonal Migrant Scheme, as the approved operators did sub-contract services and it was well known that organised crime gangs were constantly trying to infiltrate the system.
All employers we visited had very clear workplace signage around discrimination, abuse or unethical treatment. ‘Speak up’ hotlines were readily accessible either though third party providers or in-house. Other whistleblower platforms were available for people to report unethical behaviour.
Growers had a range of policies including a Human Rights Policy, Modern Slavery & Hidden Exploitation Policy, Responsible Use of Labour Providers Policy and Ethical Trading Policy. Policies are developed based on leading principles through organisations such as the United Nations, Ethical Trading Initiative (ETI) and International Labour Organisation (ILO).
Given the pervasive nature of criminal gangs targeting migrants as easy cash, fresh produce businesses were constantly on alert to signs and reports of illegal activity. Two networks have been established in the UK to assist in intelligence and to proactively disrupt labour exploitation. These include:
- Modern Slavery Intelligence Network (MSIN) – A non-profit collaboration in the UK food and agriculture sector created in response to the findings of Operation Fort, the UK’s largest ever modern slavery investigation. Its members includes retailers and producers. Intelligence-sharing mechanism to enhance the effectiveness in disrupting modern slavery and labour exploitation within the UK. Information generated by the network is used to detect, prevent and disrupt modern slavery and labour exploitation activity in their industry sector, protecting workers and improving outcomes for those directly impacted.
- Food Network for Ethical Trade (FNET) – Using the collective leverage of suppliers and retailers to bring about positive change in working conditions in global food, beverage, and horticulture supply chain. FNET creates a safe and collaborative space for food companies across the supply chain to share and learn from each other to improve human rights for workers in their operations and supply chains.
Automation
The use of automation in horticultural production is not new, however the transition to automation in recent years has been driven by lack of workforce. In some cases, machinery is no quicker or more efficient than humans but it performs a job to which there may physically be no one else to fill the role.
Machinery is often installed to undertake repetitive roles (such as putting produce in crates) or where the technology is as good (if not better) than the human thought/judgement process, such as grading product by colour.
Switching humans out of non-engaging repetitive roles into roles which require more mental stimulation is also better for the employees’ job satisfaction, as well as their health and wellbeing.
We also found that companies were proactively trying to install machinery in less appealing work environments such as where dust, temperature and moisture were negatively impacting the working conditions.
Of course, with rising input costs and cost of living putting downward pressure on retail prices, automating some roles is also seen as a cost saving measure.
Surprisingly, although many of the UK growers would say unsurprisingly, the adoption of AI and robots has made little headway either in the packing shed or on the farm. Lack of tangible progress in effective automation of traditional hand harvesting roles or some hand processing line jobs was a frustration for the sector.
Attracting local workers
Managing the needs of migrant workers is a serious undertaking and some businesses were proactively fostering much stronger connections with their local community to fill worker shortfalls. This was more evident in workplaces that didn’t have the massive upward demand for seasonal harvest labour.
In some cases the business has had strong connections to their local town or county for decades, with second or third generations of employees working for the same company. Maintaining a migrant workforce can be a costly exercise, so alternatively the business was weighing up the costs and benefits, and making packages more attractive for locals.
Some employers spoke about the benefit to local communities of keeping the wages in the local region rather than going to another country. Obviously, the feasibility of sourcing local labour was very reliant on the business, its operating model and the size and location of the nearby workforce.
Regardless of the workforce policy, all companies we visited had a very strong commitment to their local communities through a vast array of programs, projects and initiatives, including land care projects, supporting local sports teams, food donations, and school visits.
Lean management
Like automation, lean management is not a new concept. Workforce shortages, rising input costs and downward pressure on prices have all made business look to efficiencies. Lean management was however evident in nearly every facility we went to with some businesses adopting more formal certification schemes, whilst others purely adopting the principles of lean management.
‘Upsizing’ was also very evident – larger harvest and storage bins for less handling, and larger, more powerful tractors and machinery for fewer workers and less time in a field.
Data driven
The ATMAC study tour group was very fortunate to visit some of the largest and most progressive vegetable growers and processors in the UK and Europe. There were some quite marked differences between the operations we visited, however there were two areas of operations that were standouts and common to every business we went to – data and culture.
Collection, analysis and implementation of data across all the businesses was a key driver in innovation, efficiency, satisfaction, quality and success. Data was not only used to make real time decisions, but data trends informed future decisions, and was being used to make pre-emptive decision making tools.
Data was embraced as a tool that could optimise decision making. For instance, migrant worker satisfaction surveys and exit interviews could indicate what percentage of workers would return next season, why they were encouraged to return or why they were deterred from returning.
Striving to be a better business
Just when you thought that UK growers would be suffering from audit fatigue they prove you wrong! Their commitment to continual improvement, worker satisfaction, efficiency, excellence and longevity sees them voluntarily adopt additional compliance and certification programs. Below are just some of the systems we saw being adopted over and above their operational compliance systems.
- B Corp certification – www.bcorporation.net
- Investors in People – www.investorsinpeople.com
- SIX SIGMA
- Great Place to Work Certification – www.greatplacetowork.co.uk
What success looks like
In terms of workplace culture and worker welfare there were several take home messages:
- Strong family values, and history of generational family connections with employees and the community.
- Company culture that permeates through the whole organisation, from the CEO right through to the casual workers.
- Tokenistic box ticking was not part of the workplace culture – if you say you are going to do something, then do it with conviction.
- Business management system based around people, quality and efficiency – success cannot occur unless all facets of the business are addressed.
- Diagnostic tools are used to assist in evidence-based decision making.
- Operational decisions are done in consultation with HR or other areas of the business to ensure worker satisfaction.
More about the ATMAC European Study Tour
For more in-depth observations from the ATMAC European Study Tour 2023, along with photos and videos from each visit, read our blog linked below.